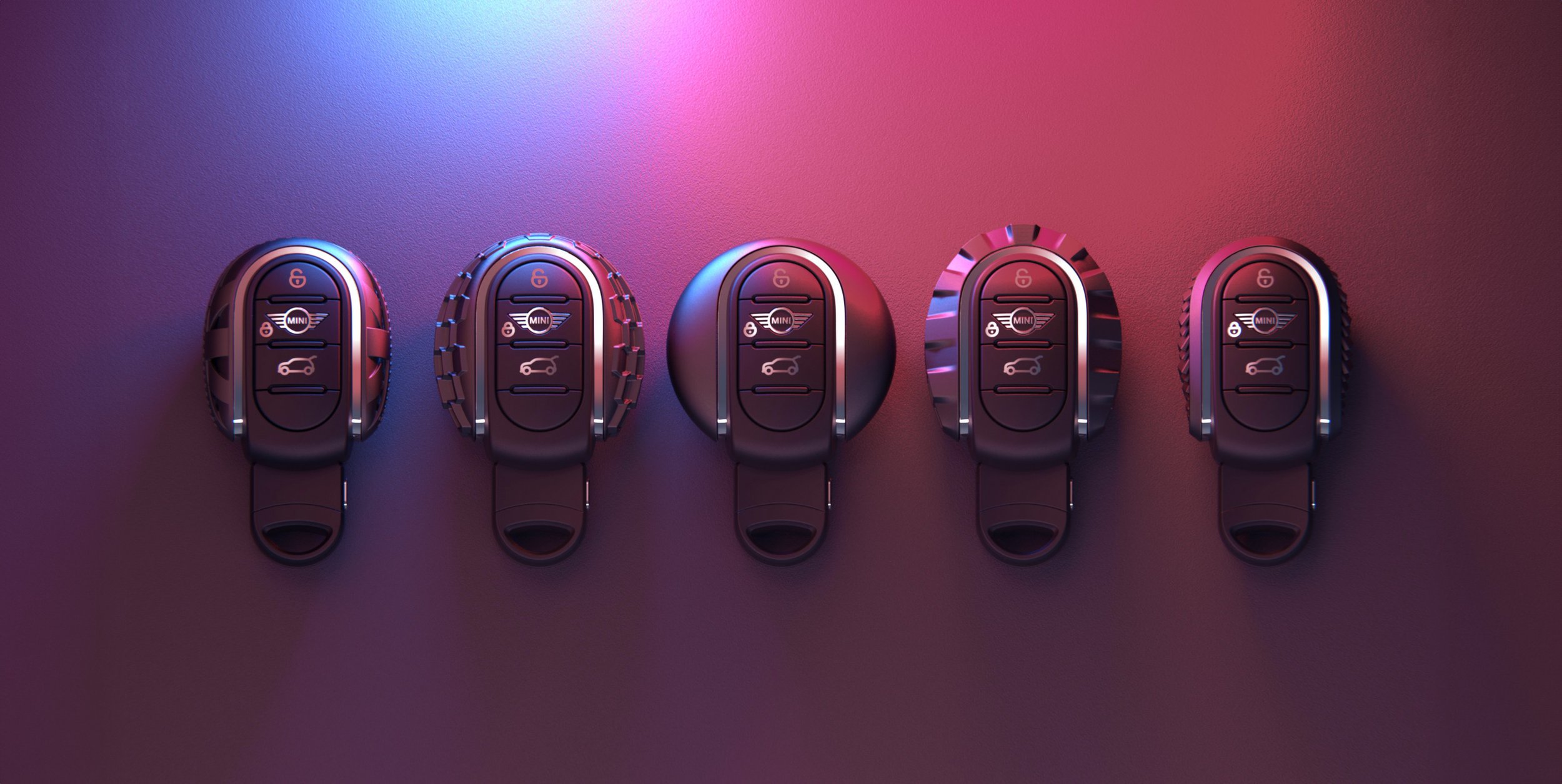
BMW Group - Mini
ADDITIVE MANUFACTURING IS DRIVING MASS CUSTOMIZATION, AND LARGE COMPANIES LIKE BMW ARE EXPLORING ITS POTENTIAL.
In our collaboration with the Mini team at BMW Group, we focused on transforming the small details that often go unnoticed into standout, personalized elements. Our goal was to create something unique and memorable.
Working together with the Mini design team, we designed and produced a series of 3D-printed key fobs, each customized for individual users, making every piece a reflection of its owner's personality. The process involved exploring various materials, colors and textures to capture the essence of Mini's brand identity while allowing for individual expression.
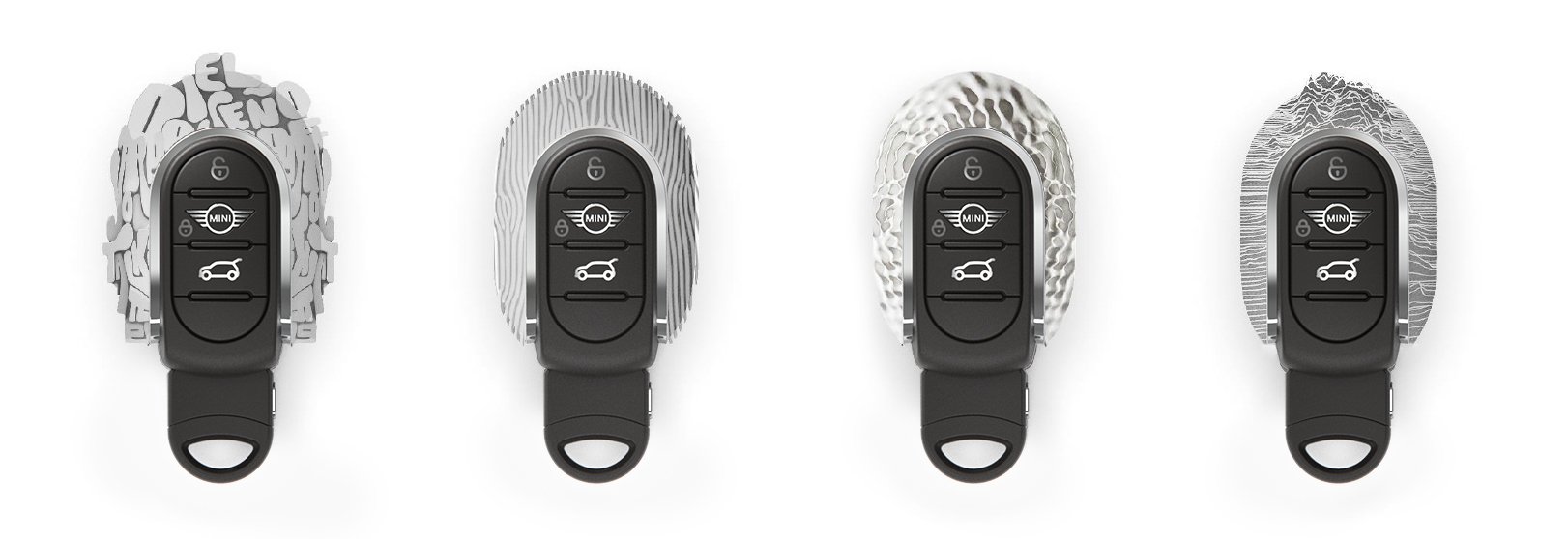
The synergy of standard modeling tools, computational design and additive manufacturing enabled us to quickly bring diverse concepts to life, including patterns, lattice structures, custom designs and their variations. This integrated approach allowed us to push the boundaries of what was possible, experimenting with complex geometries and innovative design solutions that traditional manufacturing could not achieve.
By printing components using various technologies during creative sessions, we accelerated the design process and decision-making, making it easier to validate or rule out different approaches. This hands-on, iterative workflow enabled a dynamic environment where ideas could be tested and refined in “real-time”. The result was a streamlined development process that maximized creativity while maintaining efficiency.
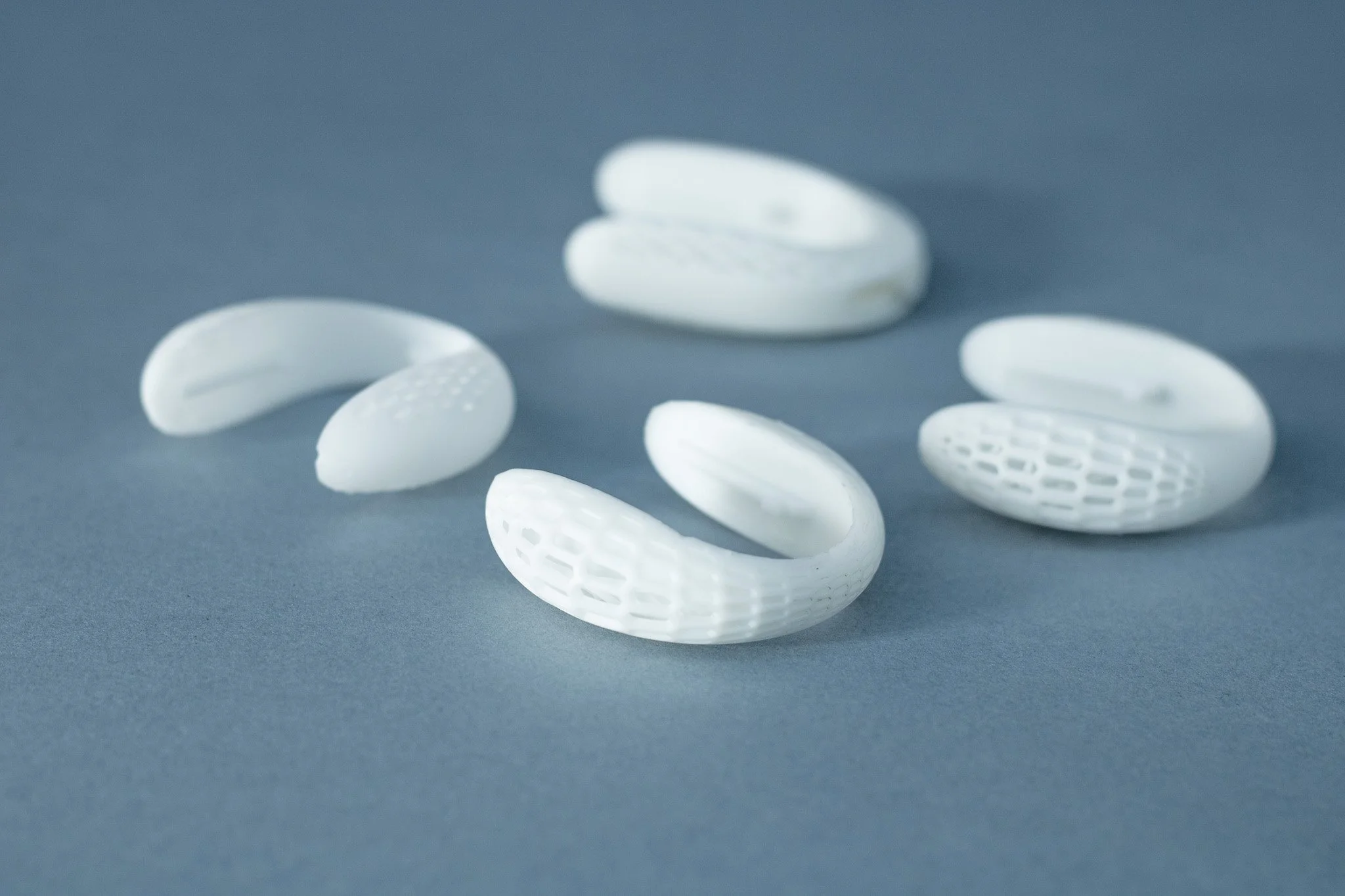

Vertical
Customer
Year
Automotive
Mini
2.020
Services
Computational Design
Parametric Design
Product design
Key Words
#Rhinoceros
#Grasshopper
#Computational Design
#Algorithmic Design